Newsletter #5 – Advanced Anti-Corrosion Coatings for Sustainable Industrial Operations
At Tetrachim, durability is at the core of every solution we provide — whether it’s recommending a coating or advising on processes. And corrosion is the first and most common challenge to tackle to extend the lifespan of industrial components. Indeed, in the industry, protecting your parts from corrosion is not just an option — it’s a necessity. At Tetrachim, we offer a full range of high-performance anti-corrosion coating solutions to help you minimize operational expenditure and maximize equipment longevity.
1 – Understanding corrosion to fight against it
Corrosion isn’t a one-size-fits-all problem. Different industries and applications are exposed to varying corrosive environments—from atmospheric moisture to aggressive chemical immersion. Here’s how corrosion severity is generally classified:

Measuring coating performance against corrosion
Corrosion protection is validated using standardized laboratory tests and real-world exposure:
- Salt Spray Test (ASTM B117 / ISO 9227):
Accelerated corrosion test using a salt fog chamber to simulate harsh environments. It is measured in hours to first sign of corrosion (e.g., >1000h = excellent) - Electrochemical Impedance Spectroscopy (EIS):
Evaluates the coating’s barrier properties by measuring electrical resistance. - Gravimetric Analysis:
Measures material loss over time in corrosive environments (mass/area/day). - Field Trials & Lifetime Data
Long-term performance documented through operational use (e.g Rilsan® with 30+ years of service in seawater).
This context is critical when selecting the right coating. Coating performance must match the corrosion level of your application to ensure optimal and long-term protection.

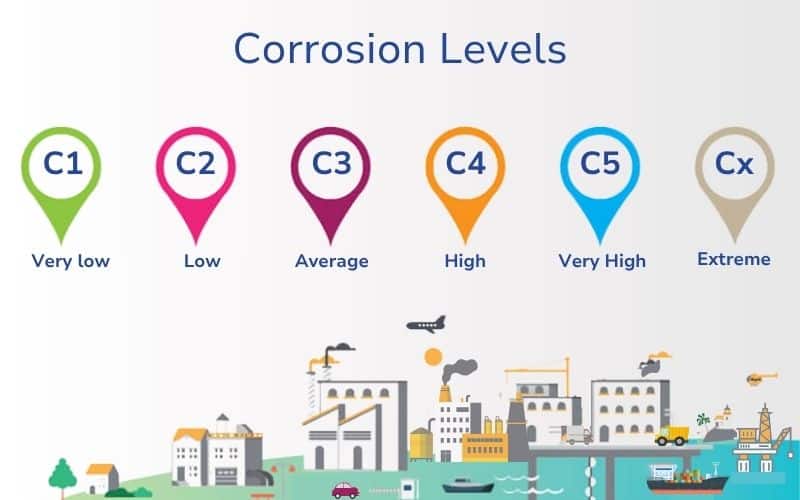
2 – Our portfolio of anti-corrosion solutions
Here’s a look at the advanced surface technologies we use to protect your equipment — even in the harshest conditions:
- Thermal Spray Coatings: Chrome & Nickel-Chrome
Thermal spray coatings using chrome or nickel-chrome alloys are particularly well-suited for environments subject to heavy wear and corrosion. This high-temperature process forms a durable metallic barrier directly on the surface of industrial parts.. - Thermal Spray: Alumina-Based Powder Coatings
Alumina forms a dense, ceramic-like protective layer. This high-purity material acts as a chemically inert barrier, offering strong resistance to both high temperatures and corrosive agents. Additionally, it provides excellent electrical insulation, making it suitable for applications involving sensitive electronic or high-voltage components. - Powder spray coatings: Rilsan® Polyamide 11
Rilsan® PA11 is among the most durable polyamide-based anti-corrosion coatings available today, especially in water-intensive and chemically aggressive environments. It has delivered over 40 years of maintenance-free performance in water treatment systems and offers outstanding resistance to chemicals such as chlorides, ozones, and industrial cleaning agents. Rilsan® adheres exceptionally well to complex geometries, including pipes, flanges, and joints, and retains flexibility over time.
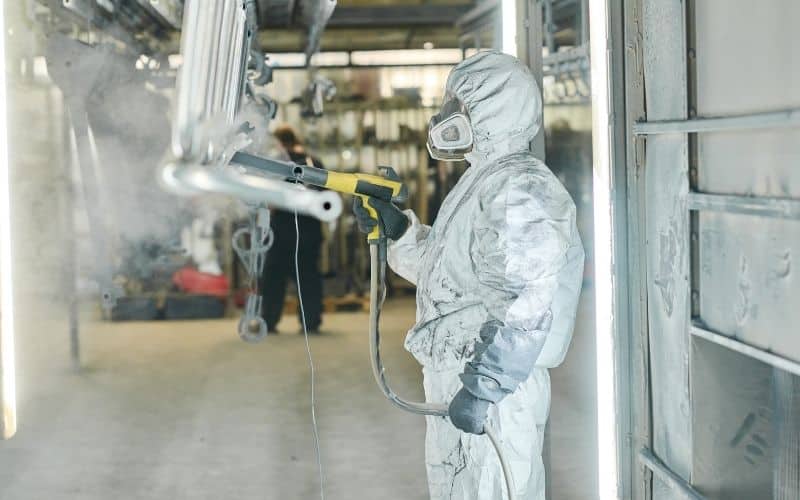
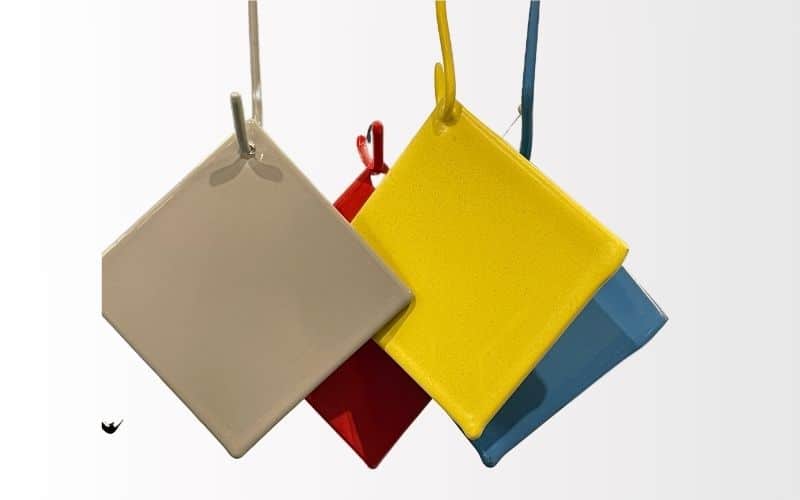
- Powder or liquid Spray coatings: Teflon™ One-Coat Systems: PTFE & FEP
Teflon™ coatings based on PTFE and FEP offer a combination of non-stick, anti-friction, and anti-corrosion properties. These one-coat systems are resistant to both heat and chemicals, making them well-suited for components such as valves, impellers, and other parts used in demanding industrial processes. - Selective Electroplating
Selective electroplating, is a targeted surface treatment method that applies Nickel, Nickel-Zinc, or Silver coatings using a specialized pad. This technique allows for localized treatment of damaged or critical areas without the need to disassemble components.
Whether it’s restoring parts or protecting new systems, Tetrachim’s coating technologies are tailored to extend the operational life of your equipment while lowering lifecycle costs. Protect more, replace less with Tetrachim coating solutions.
Contact us for a custom solution to your corrosion challenges!
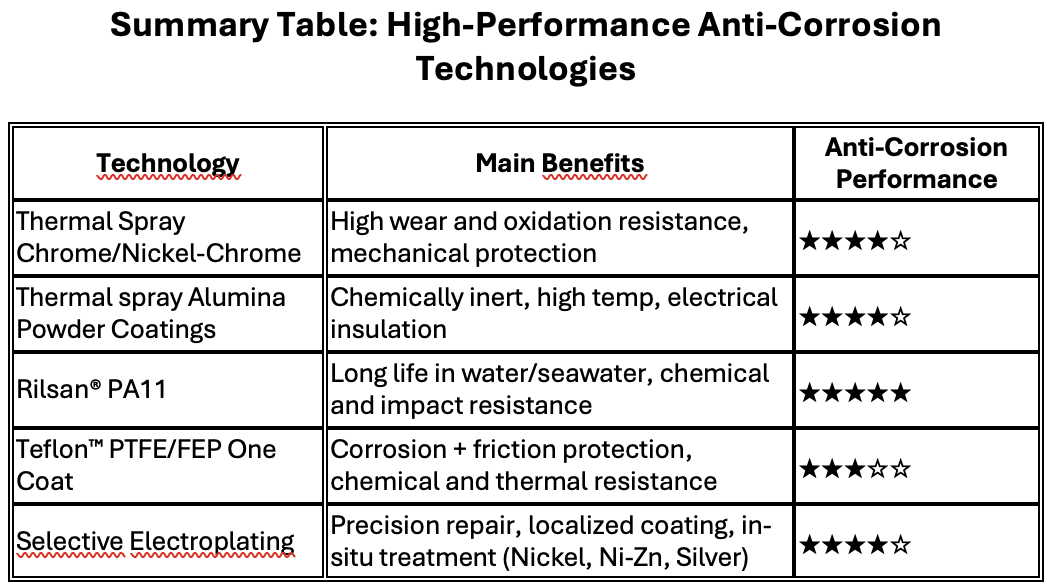