Tetrachim Newsletter #4 – Selective Electrolysis – The Smart and Sustainable Solution for Repair & Protection
Tetrachim is proud to introduce its new range of selective electrolysis products by Lorilleux, designed to offer precision, performance and sustainability. Our nickel, Zinc-nickel, copper and silver-based electrolytes enable to tackle a wide variety of applications with targeted surface treatments, ensuring superior durability and/or conductivity while reducing material waste.
The Selective Electrolysis Process
Unlike traditional electroplating, selective electrolysis allows localized deposition of metal coatings without the need for immersion baths. This targeted approach makes it ideal for both repairing worn parts and enhancing new components without disassembly or extensive preparation.

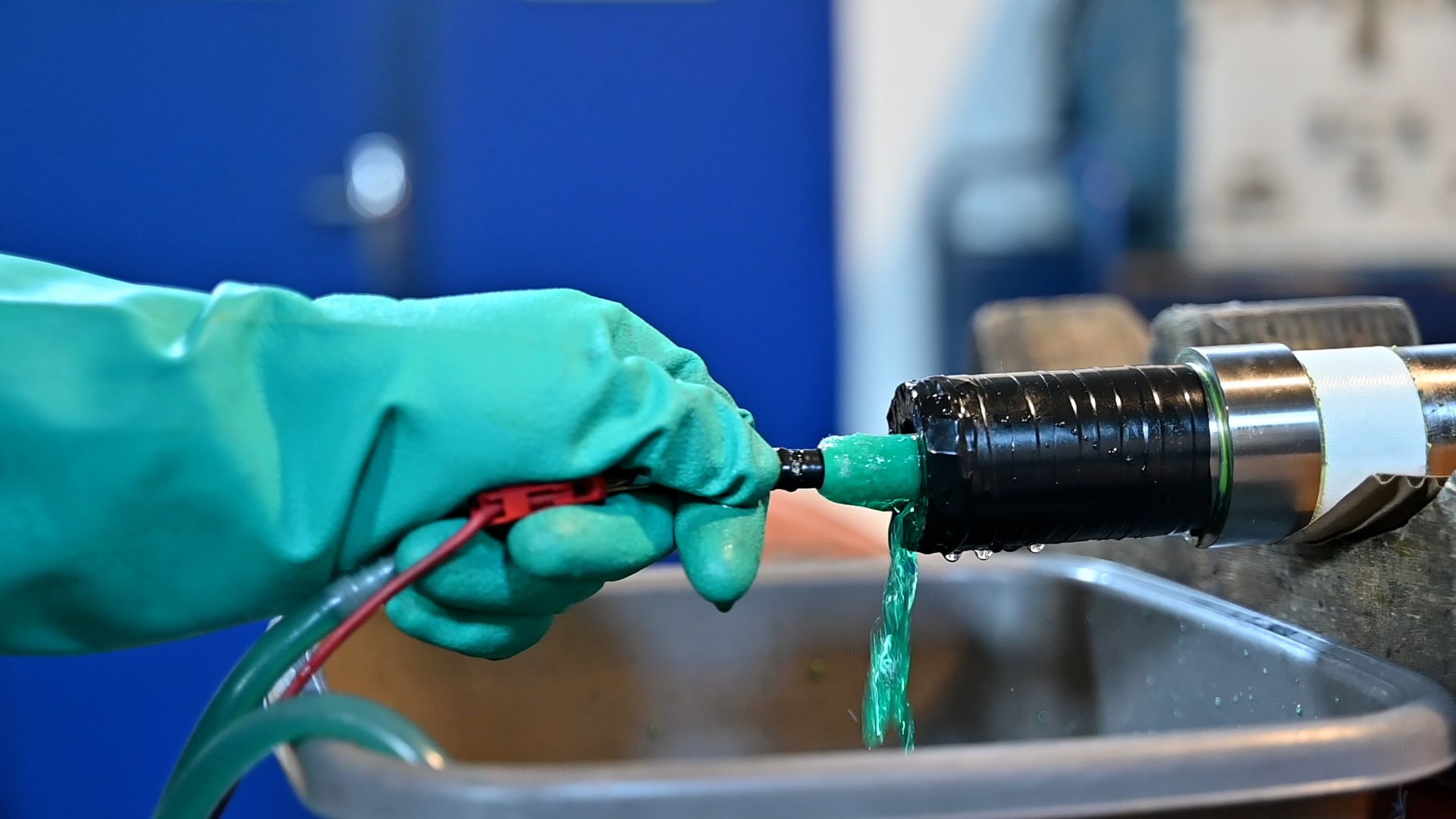
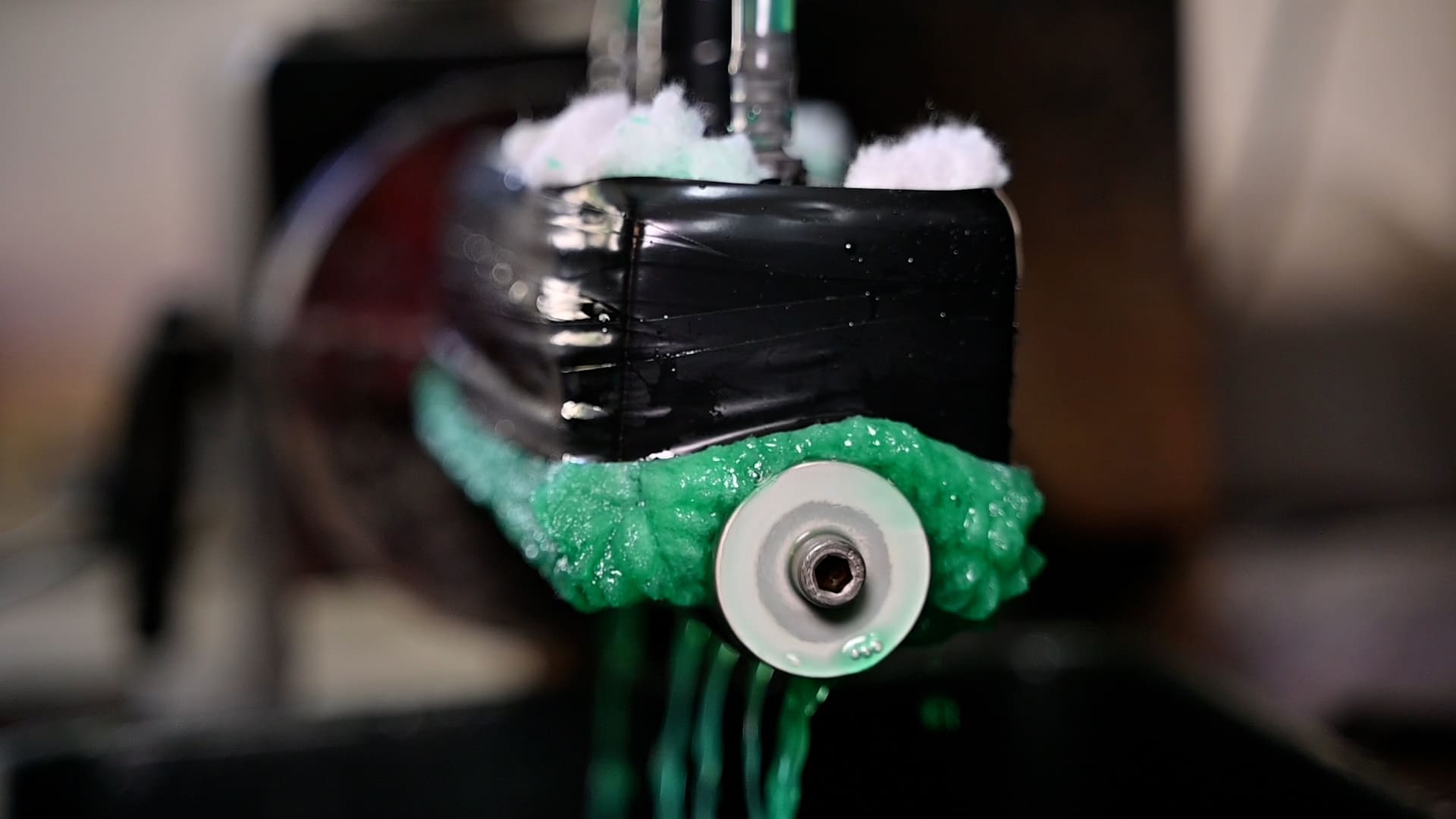
Key benefits of Tetrachim’s Electrolyte Solutions
- Selective Coatings: Our electrolytes enable the deposition of precious metals exclusively on desired areas.
- On-Site Application: The process is easily adaptable for on-site interventions, ensuring minimal downtime and operational efficiency.
- No part distortion: As treatments are conducted at room temperature, there is no risk of part distortion, preserving the integrity and functionality of the components.
- Reduced hydrogen embrittlement: The friction of the anode on the part during the process aids in degassing, significantly lowering the risk of hydrogen embrittlement—a crucial factor for sensitive components.
- Localized treatment: Selective electrolysis allows for the treatment of confined areas on assemblies that are either too large to transport or cannot be disassembled, offering unparalleled flexibility.
- Precision coatings: Coatings can be applied directly to the required thickness, eliminating the need for final re-machining and ensuring dimensional accuracy.
- Versatility with large parts: Our solutions enable to treat large components or extensive surfaces, making them suitable for a wide array of industrial applications.
Sustainability at the core of Selective Electrolysis
- Preserving valuable resources
Selective electrolysis is ideal for repairing or grinding components instead of replacing them. It therefore prevents buying new parts and using valuable raw material resources.
In addition, by coating only necessary areas to the required thickness, selective electrolysis eliminates post-treatment refinements and minimizes excess metal consumption. Optimized material usage is particularly valuable when applying precious metals such as silver.
- Lower environmental impact
Unlike traditional immersion plating, selective electrolysis eliminates the need for large plating baths, significantly cutting water and energy consumption. It also does not require large rinsing systems or excessive energy for heating solutions, making it more energy-efficient.
Since large parts don’t need to be transported to external plating facilities, selective electrolysis helps reduce CO₂ emissions associated with logistics.

A wide range of applications
To assist in selecting the appropriate electrolyte for your specific needs, please refer to the table below:
Electrolyte |
Applications |
Nickel | Corrosion resistance, wear resistance, and as an undercoat for subsequent plating |
Copper | Electrical conductivity enhancement, decorative finishes, and as an undercoat for other metal platings |
Silver | High electrical and thermal conductivity applications, decorative finishes, and antimicrobial surfaces |
Zinc-Nickel alloy | Corrosion resistance and wear resistance.Can be used as a substitute for Cadmium in aerospace applications |

At Tetrachim, we are committed to innovating for sustainability. Our select electrolyte range enables industries to achieve high-performance coatings while significantly reducing their environmental footprint.
For more detailed information or advice on our new electrolyte range or would you wish other electrolyte formulations, please contact our technical support team.